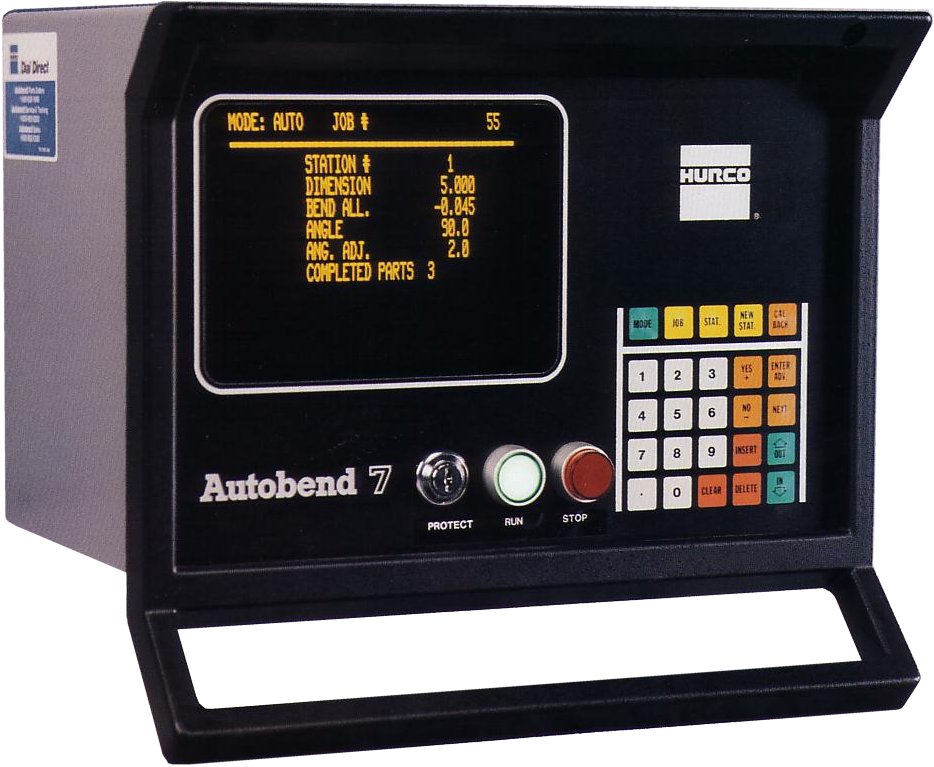
- Gain access to motor terminals. S7 gauge motor is under the left cover plate.
S6 & S8 gauges are accessed from under the gauge housing.
On LP gauges the motor is under the gauge in a metal housing.
- Disconnect both motor leads. These are the two wires closest to the pulley end of motor.
- Using a Digital Meter measure the resistance between the two terminals on the motor.
Normal reading is 1 to 3 ohms. Readings of 0 or much higher than 3 are a problem.
Rotate motor shaft and recheck in several places.
- Check the resistance between motor terminal and motor case (frame).
This should be an open circuit (infinite ohms), if less than 750K ohms this will cause failure alarms. Motion Error, Calibration faults etc… Rotate motor shaft and recheck in several places.
- There are 6 brushes total in the motor. Four for the motor & two for the Tach. Pull motor brushes and inspect commutator, if burnt & pitted the motor needs to be replaced. Check brush length, if .25” or less, or if the edges are chipped, cracked then replacing the brushes is an option. Part number for the brushes is 401 4002 003 this is for one brush.
- If the motor assy. is 8 years or older we recommend replacing the motor assy.
Part number is 001 2009 010, Motor Tach Encoder for AB6 & 7. 001 2009 004 for AB5/C
Copley AMP Check Out
- On plug to rear left side of AMP. Top & bottom Pin is power in to AMP 60VDC at Main Power on
- Same Plug middle two pins should have 60 VDC when Run Button is pushed!
- Long Plug near front of AMP is control signals. This is Numbered Bottom to Top 1 to 20
Measure Pin # 7 to 15 Should be +3.5VDC before RUN is Pushed. Should drop to zero when RUN is pushed. If no voltage before RUN is pushed then AMP is BAD. If it drops to zero volts and no LED and/or no output Volts to motor when RUN is pushed then AMP is BAD.
- If it does not drop to Zero you may have a bad Motion Module or cabling problems
Any questions please call 1-800 638 1849